"We are calling for fair competition for all packaging materials"
Karl Hagspiel, Senior Circular Economy Expert, talked in an interview with PETplanet about the recycling and sustainability strategy at ALPLA and the current challenges in the rPET market.
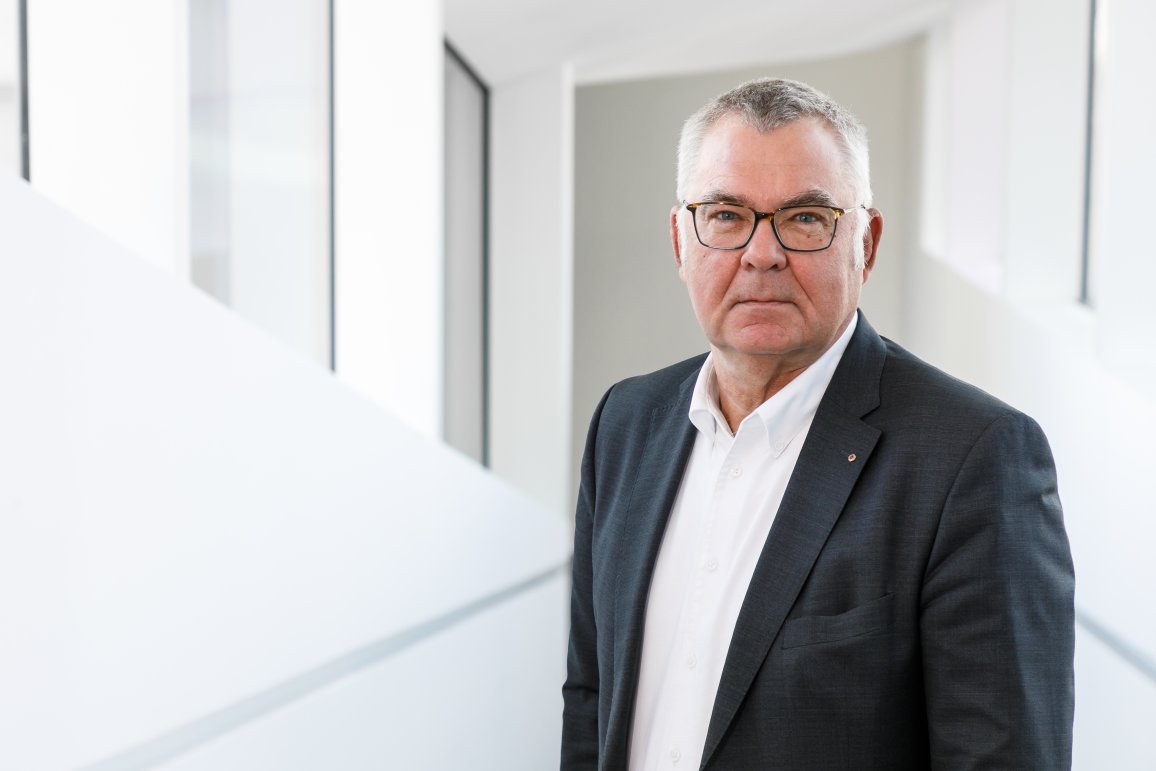
Karl Hagspiel, Senior Circular Economy Expert at ALPLA.
ALPLA has been active in plastic recycling since the 1990s. At that time, a 1,000 ml plastic bottle for Lenor was made from PCR material. Thirty-three years have passed since then. Recycling is now at the heart of a circular economy. What does a circular economy mean to ALPLA?
The circular economy is a central theme at ALPLA. Because, as the name suggests, it’s about keeping the material in the cycle or loop for as long as possible. Together with the also very important topic of design for recycling (D4R), we at ALPLA try to keep polymers at the highest possible level of recycling. But our efforts relating to plastics are only one step towards a closed loop – an approach that moves away from the prevailing linearity in the current global economy. For our part, we are trying to fulfil our responsibility by producing only 100% recyclable packaging from 2025, offering a wide variety of reusable bottles, and steadily increasing recycling capacity – for both PET and HDPE – worldwide to obtain high-quality recycled material we produce ourselves and thereby guarantee availability to our customers.
Last year, ALPLA developed Austria’s first modern PET returnable bottle for the mineral water company Vöslauer. Could you briefly outline the key data of the project and explain why Vöslauer decided on this type of returnable packaging?
The returnable PET bottle for the Vöslauer mineral water brand was the first modern returnable PET bottle for the Austrian market. In principle, we develop reusable packaging because our customers want and demand it and because we believe that this will be a big market in the future. For the project with Vöslauer, we were able to draw on our long experience in this field, because we have already been producing a returnable PET pool bottle for the German mineral water association (GDB – Genossenschaft Deutscher Brunnen) in Germany for many years. And we also have various sizes of returnable PET bottles in use for Coca-Cola in Central America. The reusable PET bottle for Vöslauer is a 1-litre bottle that, at just 55 g, is around 90 per cent lighter than the glass alternative. This alone reduces the carbon footprint by around 30 per cent. The bottle is made entirely of recyclable PET monomaterial with a recycled content of around 30 per cent. This is to be increased on a continuous basis over the coming years. With 12 cycles, the bottle is expected to remain in use for around three to four years. From an environmental point of view, the investment is already worthwhile when it is first used. At Vöslauer, the introduction of refillable PET will save around 420 t of Co2.per year. This answers the question of why Vöslauer decided to use this type of reusable packaging.
The Vöslauer returnable bottle currently contains 30% rPET. The company would like to use a higher proportion of recyclate. But since the logistics chains were reorganised after the Covid-19 pandemic in the second half of 2022, virgin PET is very cheap in Europe and is displacing PET recyclates. Inflation is also still high, which is having a negative impact on consumption. Recyclers are left with a lot of material on their hands. How do you assess the current situation?
You are right – the current price for new PET is a real challenge for recyclers, and the critical market situation is exacerbated by reduced consumption in the private sector. The first recycling plants in Germany have already had to stop production due to the current sales and price situation. But we are facing another big challenge, or rather a new danger. It is the import of rPET from countries outside the EU. The material is cheaper than the material produced within the EU. Yet we have no certainty about the origin of the material, while the EU is demanding ever stricter documentation and proof of the origin and quality of rPET or other types of recyclates. At ALPLA, we are countering this trend by expanding our own recycling plants. In this way, we want to ensure that we can continue to provide our customers with sufficiently high-quality recyclates in the future to meet the ambitious targets set by the EU and other requirements.

The returnable PET bottle for the Vöslauer mineral water brand was the first modern returnable PET bottle for the Austrian market.
For Donat Mg mineral water in Slovenia, ALPLA has developed a closed-loop system with its own recycling facilities. This closed loop makes them independent. The Slovenian government is still discussing whether and when to introduce a DRS system. In your opinion, what should a long-term strategy for the PET recycling system look like?
The deposit system (DRS) as an extended producer responsibility (EPR) model will be an integrated long-term strategy for recycling at a high level of quality. In general, what has no monetary value has no value to the individual citizen. Sorry to put it this way, but money seems to be the most effective (maybe even the only) incentive to return the bottle. In Germany, we have a 97 per cent return rate for PET bottles through the deposit system. This clearly shows that this route can work and, of course, also enables us as recyclers to get hold of more material. However, it is important that returned bottles also become bottles again and that the material is not downcycled, which unfortunately often happens at present. We will also have a DRS system for other materials – as we currently have for waste electrical and electronic equipment (WEEE) and batteries in several EU countries. France will or has already integrated EPR systems for DIY products and toys. This is a very important step towards a stronger circular economy. Why various EU member states are hesitant may be due to the projected costs of the system. But the environmental cost of ‘doing nothing’ will be much higher!
Laws and directives can provide investment security for the economy. What is your opinion on the EU directives such as the SUPD and PPWD for the plastic packaging industry? What are the challenges for relevant stakeholders such as producers, retailers and consumers?
As you mentioned, EU regulations are a challenge for the plastics industry. Currently, EU regulations focus mainly on plastic and largely neglect other packaging materials. We are calling for fair competition for all packaging materials. The only basis for accepting or banning a packaging should be the carbon footprint or, more generally, the environmental footprint of a product or packaging material. So here we are definitely advocating for eco-modelling, and we are also advocating for it at EU level. Because, for example, producing a combination of paper with a non-recyclable plastic layer just to avoid or minimize a plastic tax is the wrong way to go and does not lead to a successful circular economy. Retailers are the direct link to the consumer, and they are also affected by the SUPD and PPWR. For example, they need to offer reusable packaging. When we look at the end consumer, we need to offer them a convenient way to be part of the circular economy and raise awareness that all empty packaging is valuable raw material, even if we have to do this through a deposit scheme.
ALPLA has not limited itself to the classic PET bottle for the use of rPET. rPET is also used in thin-wall injection moulding and thin-wall extrusion blow moulding. The entire packaging market is covered. In addition to PET or rPET packaging, ALPLA is also developing alternative packaging material that is bio-based or paper-based. Which applications is the material intended for? What is the proportion of bio-based and paper-based material in current production?
At ALPLA, we are always looking for the best solution for our customers. And we have noticed that the demand for alternative material is increasing. Therefore, we are also looking for the best solution in this area. For PET, the only recycled material (rPET) that can be used for direct contact with food and nutrients, we have to meet the recycling target of the EU regulations. And with the development of thin-wall injection moulding, we are on the right track with this strategy. The question of paper-based or bio-based material is part of the same strategy. Why are we working on this? Because we are providing the solution for our customers and developing the packaging that is an integrated part of the circular economy. The paper bottle we develop must be recyclable in the paper recycling stream. When it comes to biopolymers, we have to distinguish between bio-based and biodegradable. The biodegradable materials will play a role in very specific niches, including coffee capsules or tea bags. Currently, however, these types of packaging cannot be industrially composted together with the (used) contents, tea or coffee. This is because they take longer to degrade than the turnaround time in professional composting plants. In this area, we at ALPLA have launched a coffee capsule that is home compostable – with the used contents and the fleece. However, material improvements will also solve the problem of too short turnaround times at professional composting facilities. Bio-based polymers do not have to be biodegradable, as they can be so-called drop-in chemicals (e.g., HDPE from sugar cane waste; it is absolutely identical to HDPE from fossil sources and not biodegradable). This development will continue and provide us with new biodegradable and bio-based materials, I am pretty sure of it. And our involvement in this area will also give us the opportunity to be a pioneer here. Currently, these products play a minor role in the early stages of production and use.
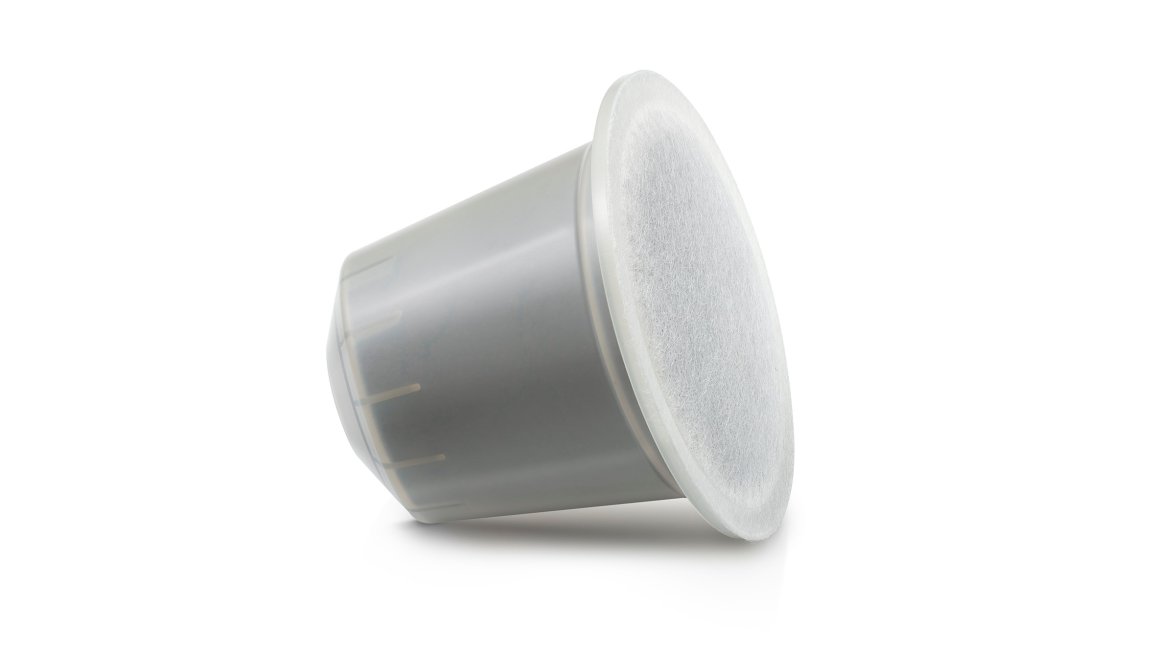
ALPLA has launched a coffee capsule that is home compostable - with used fill and fleece.
One last question for the recycling expert: recycling machine manufacturers do not see mechanical PET and/or plastic recycling at the end of its development. Improvements are still possible. So-called chemical recycling for plastics is also developing and should be complementary to other forms of recycling. There are some projects being carried out on this. A wide range of different studies is being conducted. However, this costly process needs investment, but the problem also seems to be the security of investment. The research on these processes is mainly carried out with material streams like polyolefin that have already been well prepared and sorted. This means that investments are made based on this material, including PET. How do you assess the situation and is ALPLA interested in this type of recycling?
This question is probably beyond the scope of this interview to answer. Yes, there is progress in recycling polymers, but not only in chemical recycling. Mechanical recycling is also leading to new applications and reaching new levels of quality. But let’s come back to your question about chemical recycling and investments. In chemical recycling, we have to distinguish between the technologies for polyolefins, mainly pyrolysis, and the technologies for polyesters like PET, namely metanalysis, glycolysis and hydrolysis. These are completely different technologies with very precisely defined input parameters. Today, most major oil companies and polymer producers are focused on pyrolysis. As you mentioned, investments for such plants are in the range of 600 to 900 million euros or even more and have capacities of 100,000 t per year and more. To get the green light from the board members for such an enormous investment, the legal/political environment must be clear and favourable, as well as the market, and the input stream must be clear and safe. At ALPLA, we focus on increasing our mechanical recycling capacity as we are convinced that this is the environmentally friendly way to keep the material in the cycle. At the same time, however, we are keeping a very close eye on the market for the latest developments in chemical recycling to ensure, or at least strive for, a parallel existence with equal rights. Chemical recycling should be a complementary and necessary recycling technology, but it should not interfere with the input stream that is suitable for mechanical recycling.
The interview was conducted by Heike Fischer for PETplanet.
Do you like our texts? Perhaps even so much that you want to use them in your own media? Then please get in touch with us beforehand!