Our mission: Zero Pellet Loss
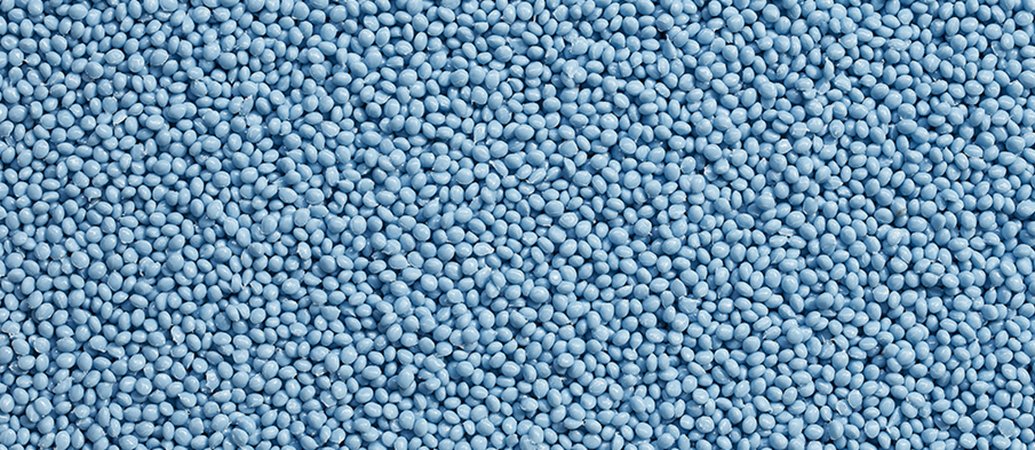
Plastic pellets are not necessarily a subject that the average person thinks about all too often. But for packaging manufacturers, it’s an essential aspect of their business. No pellets would mean no preforms, caps or bottles. Pellets are little pieces of raw plastic needed for manufacturing plastic packaging and they come in many different colours. However, their size is what can make them difficult to handle – they easily fall into cracks or behind machinery and can also get stuck in the soles of workers’ shoes.
Which is why it is important to take active steps to minimise pellet loss as much as possible, and there are programmes committed to this goal. ALPLA also wanted to take action and implemented a plan for factories and plants to help them achieve Zero Pellet Loss. It is based on the voluntary guidelines introduced by the Austrian government to prevent plastic raw materials from entering waterbodies.
What kind of measures can plants take to improve their pellet loss rate? The best way to answer this question is to visit one of the plants that has already implemented the measures. This is why our journey took us to Fussach, Austria, where we were shown around by Kerstin Ghesla, who is on the quality assurance team and is thus responsible for Zero Pellet Loss on-site.
Implementing Zero Pellet Loss
For the implementation team, the first step in the process towards Zero Pellet Loss was to examine the plant in detail. ‘Trying to achieve Zero Pellet Loss forced us to rediscover our plant, as we literally left no stone unturned,’ Kerstin tells us. During the inspection, the people on the team identified and recorded the points where granules might get lost, and then the first appliances were installed.
There are many technical and logistical changes that accompany the implementation of Zero Pellet Loss – from custom-built vacuum cleaners to a drainage system that works like an oil separator. Vacuum cleaners were also given a special nozzle that makes hoovering up granules easier. They now have their own stations spread throughout the plant – the more readily available the vacuum cleaners are, the easier it is to quickly hoover whenever workers have a free minute.
The appliances on and around the silos were inspected particularly closely, as pellets can obviously spill when pouring the material into the silos or while emptying them. Collection trays were placed underneath the docking stations, which means the lost pellets are contained within this space and can then be easily retrieved.
Our employees are also a crucial part of this process, as they work with the machinery and experience first-hand where pellet loss occurs; one employee, for instance, suggested changing the angle of the linkage at the docking station, making sure the pellets drop back into the silo when removing the tube.
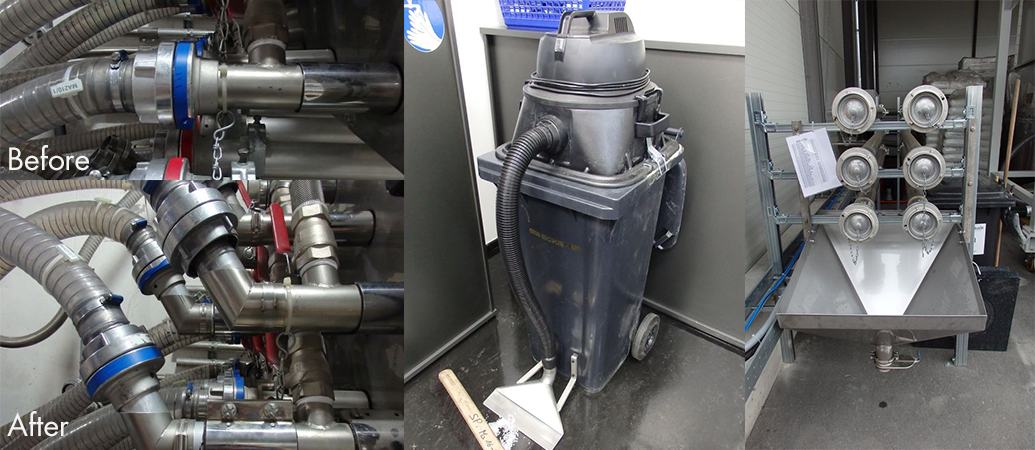
During our walk through the plant, we also saw that sifters were placed at many points to avoid the granules from entering the sewage water. For those few that do manage to find their way into the sewage water, a system was installed in which the water reaches a tank where the drainage pipe is situated in the middle. Polyethylene (PE) and polypropylene (PP) float on top because they are lighter than water. Polyethylene terephthalate (PET) sinks to the ground, meaning the granules stay in the tank and do not make it through the pipe that is placed midway.
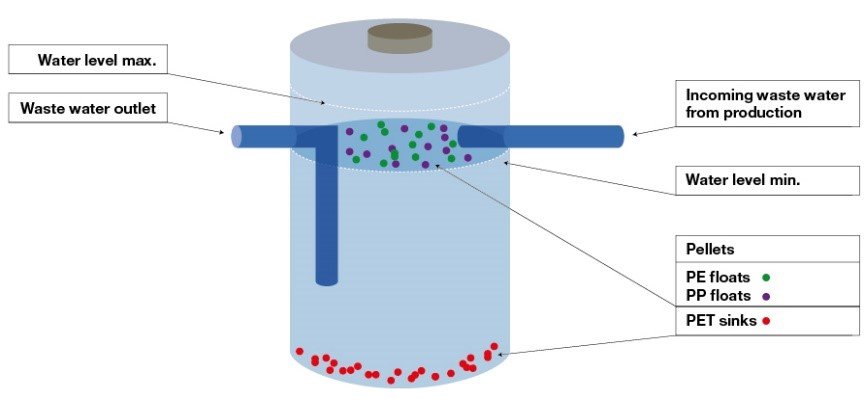
The project devoted to Zero Pellet Loss is an ongoing process, and new measures are constantly being added. The examples above clearly demonstrate how the smallest changes can make a difference. And the best thing is that it’s a project everyone can actively get involved in, thus contributing to environmental protection. Luckily for us, the general awareness of this issue has definitely increased over the past years. This attention contributes positively to our mission, as people view the prevention of litter as an increasingly significant issue. The more people are involved, the bigger difference we can make – and the more pellets we can save.
Do you like our texts? Perhaps even so much that you want to use them in your own media? Then please get in touch with us beforehand!