In-house plants: next door to the customer
Collaboration with customers which is based on partnership offers environmental and economic advantages.
Close to half of all ALPLA sites are in-house plants. Here, we produce packaging solutions right next to where our customers are based – resulting in both environmental and economic advantages. In May 2019, we inaugurated the ‘world’s biggest recyclate bottle production line’ at the new production facility belonging to Werner & Mertz in Mainz.
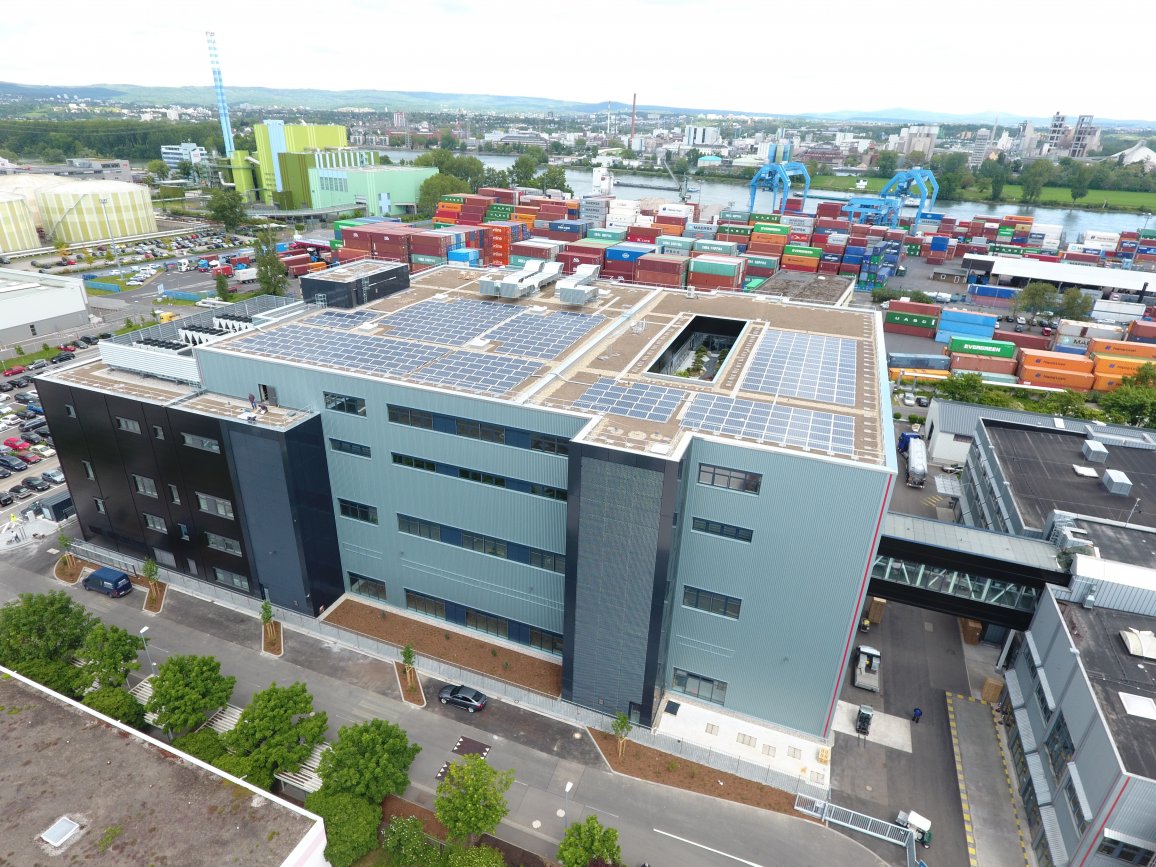
Founded in 1867 as a wax goods factory, Werner & Mertz now specialises in cleaning and care products. This family-owned enterprise has earned itself a reputation not only thanks to the high quality of its products, but also and in particular because of its systematic sustainability strategy. Indeed, company owner Reinhard Schneider is considered a pioneer of sustainability in Germany. ‘Nowadays it is certainly technologically possible to develop highly effective products – in our case that means strong cleaning products – that satisfy the highest environmental standards along the entire value chain,’ he is quoted as saying on a company website.
Bottles made entirely of recyclate
Intelligent packaging solutions with as large a recyclate proportion as possible are an integral part of the company’s philosophy. And this is where ALPLA comes in: we have the honour of counting Werner & Mertz among our customers since 1995 and have been producing bottles for cleaning and care products for them in Mainz since that time. This long-standing collaboration has turned a business relationship into a partnership founded on the same values and goals. For example, ALPLA plays an active part in Werner & Mertz’s recyclate initiative, the aim of which is to keep recyclables collected from households in Germany (in ‘Gelber Sack’ yellow bin bags) within the cycle and to turn them into new packaging. We contribute our expertise in the areas of producing recycled plastics and processing these materials into fully functional packaging. Thanks to its comprehensive commitment, bottles made entirely of recyclate are now par for the course for the cleaning agent specialist. A total of 266 million bottles made entirely out of recycled plastics as at May 2019 attest to this!
Energy-efficient construction
The design of the production process can have a major impact on just how sustainable a product really is. Werner & Mertz realised a sophisticated concept when planning their new L8 production facility. The building’s details read like a manual on state-of-the-art and energy-efficient construction – recycled concrete, photovoltaics, heat recovery, district heating, LED lighting, and so on. The output of the photovoltaic system on the roof comprising 455 modules is impressive in itself: the system’s annual yield is 109,000 kilowatt-hours, which equates to an annual carbon reduction of 76.3 tonnes.
ALPLA moved into this building together with the customer. ‘In building this new production centre, we have created the world’s biggest recyclate bottle production line,’ declared the owner of Werner & Mertz, Reinhard Schneider, at the inauguration ceremony in May. ALPLA CEO Günther Lehner emphasised: ‘We are very pleased about the long-standing and trusting cooperation with Werner & Mertz. We have invested 13 million euros to ensure state-of-the-art and efficient packaging production in the new production centre.’
Everything running like clockwork
Last, but not least, here are some of the details of our in-house production facility in Mainz. Thanks to ALPLA’s many years of experience with these solutions – ALPLA inaugurated its first in-house plant in 1968 – we are able to realise projects of this kind swiftly. Werner & Mertz handed the building over to us in September 2018 and we began to put all the infrastructure in place that same month. The first pieces of machinery then followed in mid-December and all the work was completed in April 2019.
Preform and bottle conveyance is fully automated. 20 conveyor belts across five production lines with a total of 225 running metres deliver optimised logistics. Our air compressors are equipped with a heat recovery system, meaning around 96 per cent of the energy used can be put to use a second time. The ventilation system featuring air extraction from the machines and in material processing likewise features highly efficient heat recovery, resulting in lower energy needs and costs.
Aside from the facts and figures for this modern production facility, we are very proud to be working with an exemplary company like Werner & Mertz. The long-standing partnership offers clear environmental advantages, and an in-house plant also cuts costs and saves time. But the key for both parties is that they are familiar with one another and that there is mutual understanding of the other party’s needs, thereby keeping the door wide open for future improvements and developments.
Fact box: The benefits of in-house plants at a glance
- Reduction in the outer packaging needed for shipment
- Truck transport is eliminated entirely, thus reducing carbon emissions
- Bespoke logistics solutions
- Bottle production is directly connected to the customer’s bottling facilities
- Minimum storage space required
- Cooperation flexibility, further developments are accelerated
Do you like our texts? Perhaps even so much that you want to use them in your own media? Then please get in touch with us beforehand!