Start of single-use deposit in Austria
From 1 January 2025, a deposit of 25 cents will be charged on all new single-use plastic and metal beverage containers from 0.1 to 3 litres in Austria. What does this mean for manufacturers, consumers and the circular economy?
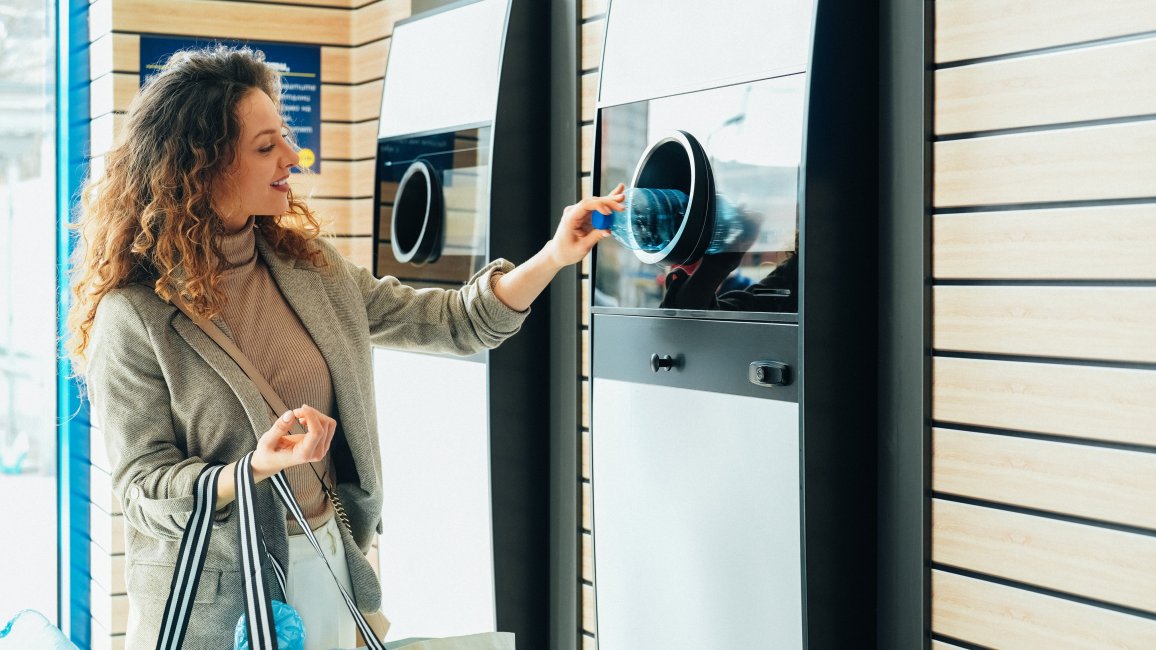
From 1 January 2025, PET bottles in Austria will be returned to the point of sale - whether supermarket, bakery, kiosk or snack bar.
Less littering, appreciation for plastic and more sustainable packaging: The new deposit system in Austria aims to achieve all of this. From 1 January 2025, all single-use plastic bottles and metal cans for drinks with a filling volume of 0.1 to 3 litres that are placed on the market in Austria will have to have a deposit. This means that PET bottles with a deposit logo and barcode will no longer belong in the Yellow Bag. Instead, they will be returned to the point of sale - whether supermarket, bakery, kiosk or snack bar. The most important requirements: The bottle and label must remain intact. Money back is only available for machine-readable packaging. In future, bottles and cans will therefore only be mechanically compressed after they have been returned.
The deposit system is regulated by a central organisation, EWP Recycling Pfand Österreich gGmbH. It acts on behalf of the Ministry of Climate Protection and is owned by a supporting organisation. Its members are the Association of Austrian Beverage Producers, the Federal Committee of the Food Trade and numerous manufacturers and take-back organisations. The small g stands for non-profit in German and refers to the purpose of the organisation: society as a whole benefits from its commitment to the environment and is itself responsible for its success.
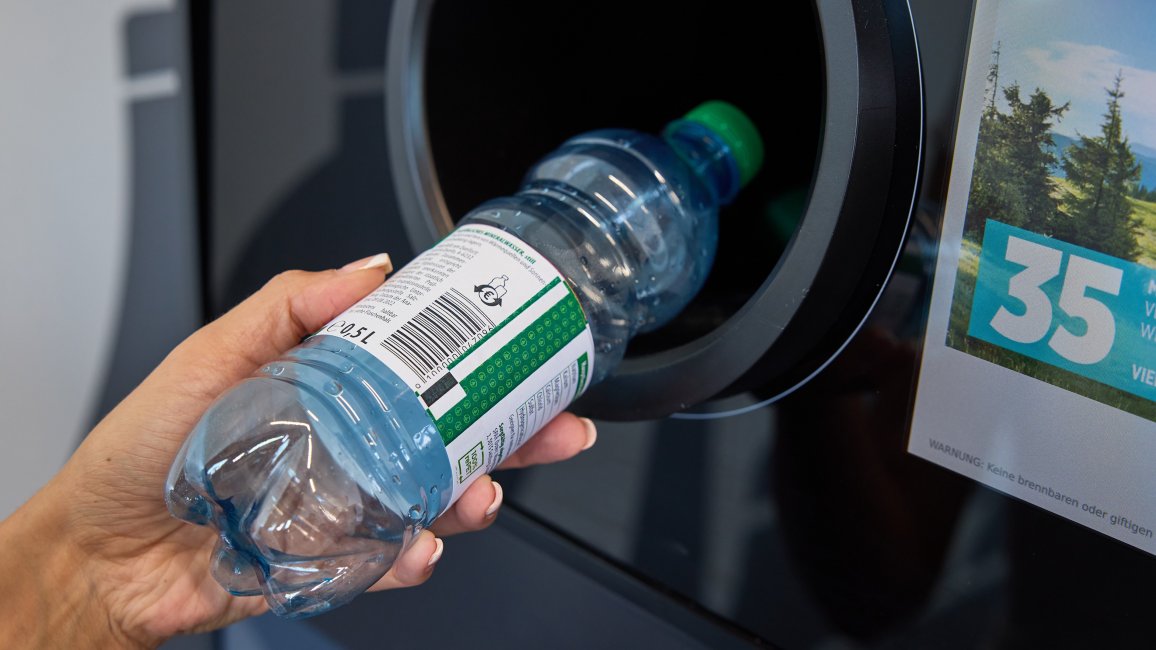
The deposit logo and barcode on the label must remain intact. Money back is only available for machine-readable packaging. Photo credit: SPAR/APA-Fotoservice/Schedl
Security for manufacturers
The deposit system aims to increase the collection rate from the current 70 per cent to 90 per cent by 2027. The new handling of defined beverage packaging - there are exceptions for composite cartons, milk and syrup - serves the objectives of the new EU regulations Single-Use Plastics Directive (SUPD) and Packaging and Packaging Waste Regulation (PPWR). The recycling material quotas prescribed therein are among the biggest challenges facing the food industry. The deposit system provides an indirect remedy.
More returns also means more material for recycling, which is a huge advantage for manufacturers. In Austria - unlike in Germany - they have a right of first refusal at standard market prices. This applies to 90 per cent of the collected and sorted material. An example: 900 tonnes of 1000 tonnes of transparent PET end up at the central organisation with the target collection rate of 90%. The producer is entitled to 90 per cent of this - i.e. 810 tonnes. ‘This ensures the long-term supply of food-grade PET recycling material and helps manufacturers fulfil their quotas,’ says Karl Hagpiel, Senior Circular Economy Expert at ALPLA. After purchase, the pressed bale goods are sent on to the recycling plant of choice - for example to the ALPLArecycling plant in Wöllersdorf.
Good and bad packaging
The proceeds from the sale of the collected recyclables finance the deposit system and the handling fee of a few euro cents per packaging. Other sources of funding are the ‘deposit slip’ for non-returned bottles and the producer contributions from distributors. These vary depending on the type and characteristics of the packaging. If a container falls into one of the performance classes C to E during ecomodulation due to materials, colours, barriers, labels, adhesives or printing, surcharges are due. If material-specific recycling incompatibilities such as additives are used for PET bottles, class E and a surcharge of 60 per cent automatically apply.
Design for recycling therefore pays off, as Hagspiel emphasises: ‘The majority of our products are in classes A and B. We are working towards this when advising our customers and are already setting the course for 2026.’ The second stage of ecomodulation will then come into force. It will include criteria such as size coverage, resource consumption and the new CEN standards expected in 2025 for assessing the recyclability of packaging. Non-wet-strength paper labels will then be categorised as material-specific recycling incompatibility for PET bottles.
Do you like our texts? Perhaps even so much that you want to use them in your own media? Then please get in touch with us beforehand!