The production of pharmaceutical packaging
The production of so-called primary packaging, which comes into direct contact with drugs, is particularly demanding and requires compliance with high-quality standards with regard to the purity of the products. This blog post gives an insight into the cleanroom production of ALPLApharma in Greece.
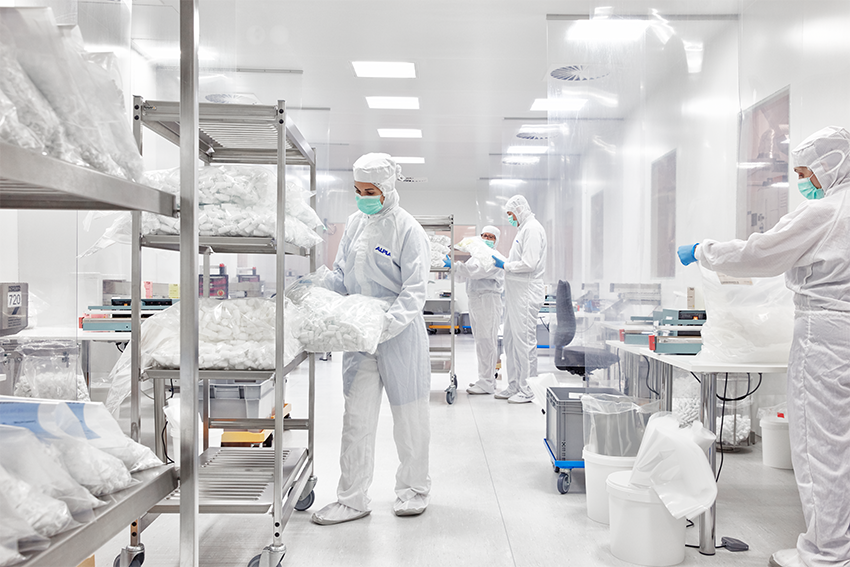
Packaging for the pharmaceutical industry has been manufactured in Koropi, southeast of Athens, for more than four decades. Long-term, trusting relationships with customers and suppliers have emerged. All sides benefit from the experience and competence in this area. In 2018, this was an important reason for ALPLA to take over the locations of the company ARGO S.A., which specialized in packaging solutions for pharmaceuticals and personal care. The philosophies and corporate cultures of both companies matched very well. The cleanroom competencies of ALPLA for the pharmaceutical market are now bundled at the Greek location.
Demanding products
There is a concentrated and disciplined atmosphere within the cleanroom of ALPLA in Koropi. No wonder when you consider that high-quality packaging for sensitive pharmaceutical industry products is produced here around the clock in a three-shift operation. Specifically, it involves dropper systems, consisting of a cap, undercap and a bottle. The dropper systems are used, for example, for ophthalmic products. The third expansion phase of the cleanroom was recently completed. In the course of this, the capacity of the cleanroom was increased by about 30 percent.
Production and packaging
Different processes are used for production, depending on the component. Injection moulding machines produce the closures and undercaps (IM process); injection blow moulding machines manufacture the bottles (IBM process). Production takes place fully automatically right into the cleanroom. Strict procedures apply here. The number of products is recorded automatically. The components arrive directly from the conveyor belt into prepared plastic bags. The bags with the products are then sealed, labelled and packed in a second or even a third bag according to the requirements of the final application. In between there are regular quality checks with regard to material (purity), opening torque and tightness. Sterilisation then takes place in external validated sterilisation sites (using ethylene oxide or gamma irradiation) before the packaging solutions are finally delivered to the customer.
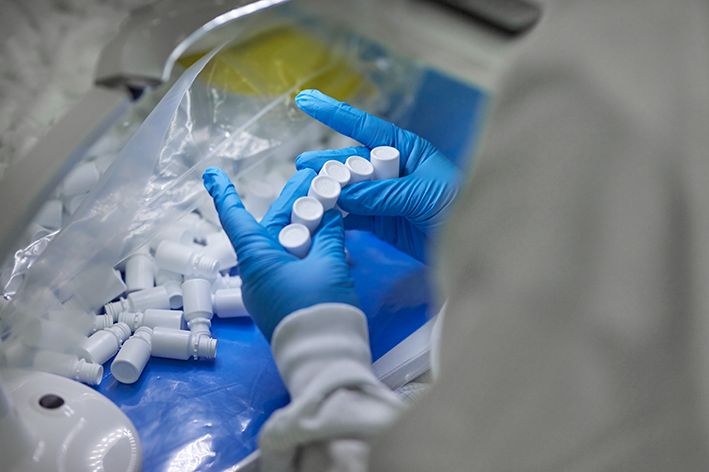
Special requirements for employees
The number of airborne particles in the cleanroom must be kept as low as possible in addition to the structural requirements, and humans are usually the greatest source for particles and other contaminants. As a result, appropriate cleanroom clothing with hoods and covers for the shoes are important. The employees in this area are carefully selected and trained in order to take special care and have a high level of self-discipline. It is this consistently high commitment to excellence that distinguishes the employees and their work in the cleanroom area.
Manufacturing according to high standards
The requirements for rooms in which primary packaging is manufactured that is in direct contact with drugs are very high. Impurities or a certain number of particles in the air lead directly to the fact that the packaging is unusable in terms of product safety. Therefore, the production on-site is conducted according to the following international standards:
- ISO cleanroom class 7 according to ISO 14644-1: Standard that defines specific requirements for the cleanliness of the room, the production process, the employees and their workplace.
- ISO 15378: Standard for Good Manufacturing Practice (GMP) of primary packaging for medicinal use based on ISO 9001. It applies specifically to manufacturers of packaging materials for pharmaceutical products.
- ISO 13485: Standard to prove an effective quality management system for medical device manufacturers.
About ALPLApharma
ALPLApharma consolidates the pharma portfolio of ALPLA with the main production plants being in Greece, Romania, Egypt and South Africa. The current product portfolio ranges from bottles for liquids and solids, and containers for tablets and pills to closures and dispensing systems – especially eyedroppers and nasal sprays – as well as devices for administering medication with and without a measuring function.
Further information and the complete product catalogue can be found on the ALPLApharma website.
Do you like our texts? Perhaps even so much that you want to use them in your own media? Then please get in touch with us beforehand!