Together we are bringing the bio-based paper bottle to market maturity
An interview with Florian Müller, CTO of Paper Bottle Company.
In April 2019, ALPLA and BillerudKorsnäs, the leading Swedish provider of paper packaging materials and solutions, announced that they were starting a joint venture for the development of a paper bottle. This joint venture is now an established company by the name of Paboco (Paper Bottle Company).
Thanks to its owners, the start-up already has two strong partners in the background and, in addition, Paboco has built up a considerable network with its ‘Pioneer’ community. Together with the Pioneer brands Carlsberg, L’Oréal, Coca-Cola Europe and Absolut as well as its technology partners, Paboco is working intensely on realising its long-term objective: the development and scaling of a fully bio-based, recyclable, fibre-based bottle made of renewable materials.
Paboco CTO Florian Müller sheds light on the next steps and the associated challenges in the interview below. The 32-year-old took the lead role at ALPLA for the preparations for the joint venture. He has been Chief Technology Officer (CTO) at Paboco since September 2019.
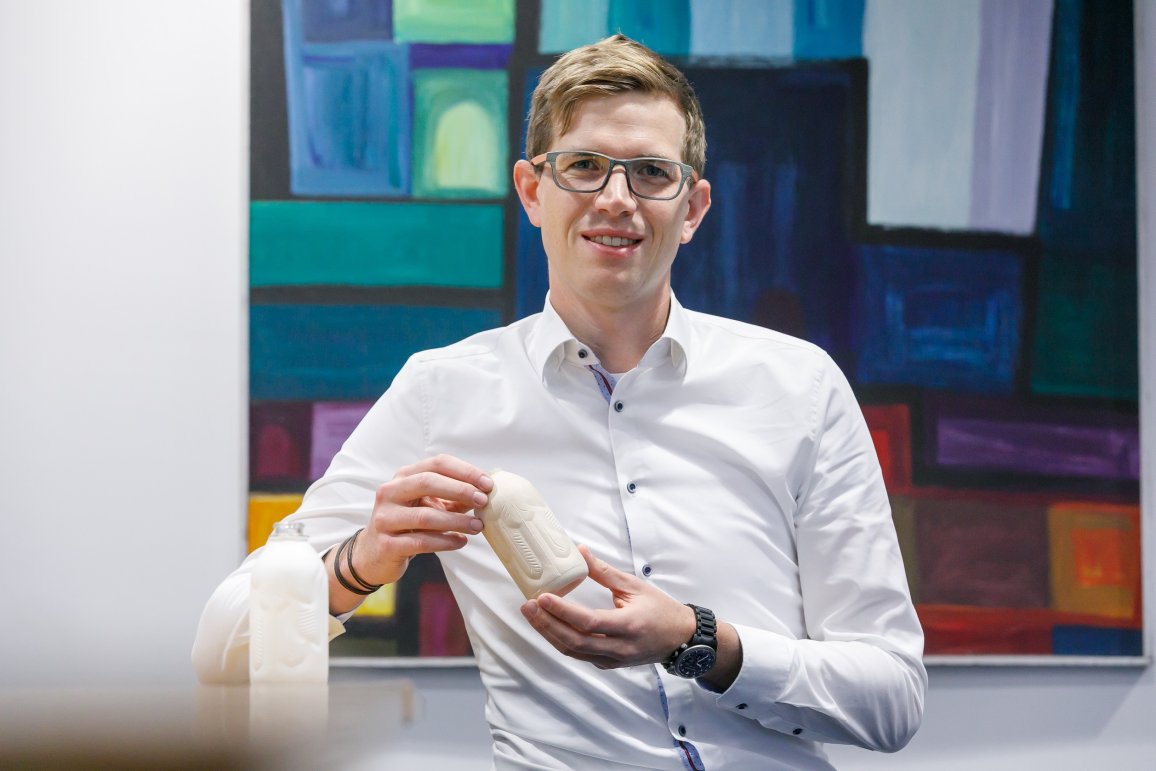
Florian, why is it that an internationally recognised plastic packaging specialist such as ALPLA is investing in a joint venture that has a goal of developing a paper bottle? Does that signify a move away from plastics?
ALPLA is a manufacturer of packaging and produces rigid packaging made of plastic for a wide variety of market segments. The technology that ALPLA has gained access to through the joint venture also enables the manufacturing of a rigid body and is very similar to what the family-owned company has been a leader in for 60 years. This is more of an expansion of the ALPLA product portfolio rather than a move away from plastic, and represents a complementary solution. In future, the paper bottle could act as an additional wise option in order to offer a packaging solution that is the ecological best in its area of application.
Nevertheless, paper and plastic could not be any more different as materials…
Paper of course has completely different characteristics from plastic, though also offers different possibilities. Additionally, we first need to establish whether the technology can be developed far enough that we can produce relevant volumes of it economically and play in a comparable league to the plastics industry. This is also strongly dependent on the goods inside the packaging. In my opinion, many products will likely have to rely on a plastic-based packaging solution for a long time yet so that the transport, safety and quality of the packaged product is guaranteed through to the final consumer. Plastic will be unable to be replaced in certain areas of application due to its functions.
What role does ALPLA have in the joint venture and the development of the paper bottle?
ALPLA is playing two roles. For starters, ALPLA is an owner and therefore financial backer, while secondly ALPLA is playing a key role when it comes to the technology. We are contributing our expertise in the creation of production capacity on a robust, scalable basis. That means we are making sure that production processes stabilise and that we are in future able to manufacture volumes that are relevant for the market. Finally, Paboco could use the ALPLA Group network of existing production sites as partners and offer production worldwide at various locations.
What is the current technological progress? What are the challenges at the moment?
Current we have a prototype machine which we are using to manufacture test quantities for our Pioneer brands whilst developing the process. At the same time, the machine is not quite robust enough yet, which is posing a challenge. We have to be able to analyse and understand problems conscientiously and also work with the material’s characteristics better. Pulp behaves fundamentally differently from plastic. So, in this respect, we are looking for a suitable supplier of the optimal parts. However, there are things we are benefiting from. Namely, the fibre industry has a long history and the right products do exist, though we need to find the right partners.
Something that is completely new to the fibre industry, on the other hand, is the manufacturing of rigid bodies – in the third dimension. There are several core issues related to this that we have to solve internally – in the places where we deviate from other manufacturing methods. We are undertaking intensive research and development on this.
Paboco launched the first generation of the paper bottle in October 2019. However, this generation still has a barrier made of plastic. In what direction will the barrier’s development continue?
We are very much working in line with our vision – Paboco is seeking to develop a 100 per cent bio-based paper bottle that is able to hold and protect liquids. We still need to develop certain components for this. In the meantime, we are currently working on the first and second generations of the paper bottle with a plastic barrier layer so that we can still make crucial progress. In the first generation, this barrier will be made of fossil-based materials such as PET or recycled PET. However, for the second generation, we are working with our technology partner Avantium on a barrier made of bio-based PEF. On top of that, ALPLA was able to deliver a solution for the first generation’s internal layer extremely rapidly. That is how it was possible for us to serve the first beer from first-generation paper bottles at the C40 event in Copenhagen at the beginning of October 2019.
However, our goal is not to implement this on a large scale. Instead, we aim as far as possible to develop barriers for 100 per cent bio-based fibre packaging. Developing a barrier for such fibre products currently resembles the search for the holy grail. I am convinced that the company that pulls it off and develops a smart solution will set off a massive shift in the packaging industry.
The third generation will be the 100 per cent bio-based, recyclable packaging solution that will also be biodegradable in the right circumstances. However, that is an objective that we do not want to emphasise overly. We want to keep materials in circulation and not suggest to consumers that it is OK for packaging to end up in the environment.
Does that mean you are concerned that the fast biodegradability of such packaging solutions downplays or even encourages littering?
We are thinking in terms of the circular economy. Fibres are an important raw material; the waste paper industry relies on primary fibre flows. We can make a good contribution to this with the paper bottle. Naturally we are not developing this packaging solution to combat littering, that would be absurd. However, if the packaging ends up in the environment, it won’t damage nature for long since it can decompose into its core parts.
Back to the third generation – when will we see these paper bottles on the market?
I think that we will see prototypes relatively quickly, but progress won’t stop with the development of the third-generation barrier. We also need a matching cap system and must ensure that everything is scalable while remaining economical. Overall, I am very confident. We are learning incredible amounts and I’m very happy that ALPLA is participating in this joint venture and that I personally also have this opportunity.
Having the Pioneer community should also help accelerate the development of the paper bottle.
Yes, we have an extremely good set-up and heavyweight network for realising our objective. We have a technology developer and converter and a materials supplier collaborating very closely with ALPLA and BillerudKorsnäs. The Pioneer brands, including Carlsberg, L’Oréal, Coca-Cola Europe and Absolut, are also making a significant contribution. These highly regarded companies are prepared to support the product and put it on the market. This establishes relevance in the market and, secondly, brings the benefits of this new packaging solution closer to the final consumer. Our technology partners Avantium and Teknos are delivering solutions – particularly for the barriers – and adapting them to our needs. We intend to make things happen more quickly through this collaborative partnership, in which each party is an expert in its field and in which we can use the synergies together.
How will you ensure that these bottles have optimal recyclability? Can they be disposed of with waste paper? Do the bottles have to be sorted into their own recycling compartment?
We of course aim to produce a recyclable bottle that can be integrated into existing recycling flows. We are focusing on the paper flow because the third generation is planned to be fully plastic-free. That means developing the bottle for the plastics sack or plastics bin would be the wrong approach right now. Based on the conversations that we’ve had, the first-generation paper bottle is suitable for the waste paper flow, though perhaps not completely optimal. This entails the plastic being separated from the paper, with the latter being processed back into pulp. Carlsberg currently has a clear intention of charging a container deposit for the bottle. It has good reason for doing this, seeing as container deposit schemes are well established in Scandinavia and enjoy high acceptance among consumers.
Do you like our texts? Perhaps even so much that you want to use them in your own media? Then please get in touch with us beforehand!