In-house production drastically reduces CO2 emissions
Around the world, ALPLA operates 71 of 181 production facilities as in-house plants, right next door to the customers. These plants avoided around 43,000 tonnes of CO2e in 2019, which is the equivalent of 13,000 flights from Vienna to Rio de Janeiro.
It is currently being traded as the ‘new currency’ because its significance – or better said, its impact – is so vastly important in our times: CO2. Carbon dioxide and other greenhouse gases are responsible for global warming. This warming has to be – and for experts, this is a certainty – curbed as swiftly as possible. Otherwise it will end in a climatic catastrophe with a devastating impact on our planet, such as droughts or rising sea levels.
Transport and energy and heating supplies produce the most greenhouse gases. Whoever reduces the production of these gases is making a significant contribution to counter climate change. ‘From this perspective, we have looked at our in-house plants and come to a staggering conclusion,’ reports Linda Staib, Sustainability Manager at ALPLA. ‘Our 71 in-house plants avoided 43,000 tonnes of CO2 or carbon equivalent in 2019.’
The following comparisons prove that 43,000 tonnes less CO2e is a significant contribution to climate protection: 43,000 tonnes of CO2e are the equivalent of what 2.13 million trees would take from the air. You could also take the train from Munich to Berlin and back 1.3 million times or fly from Vienna to Rio de Janeiro 13,000 times.
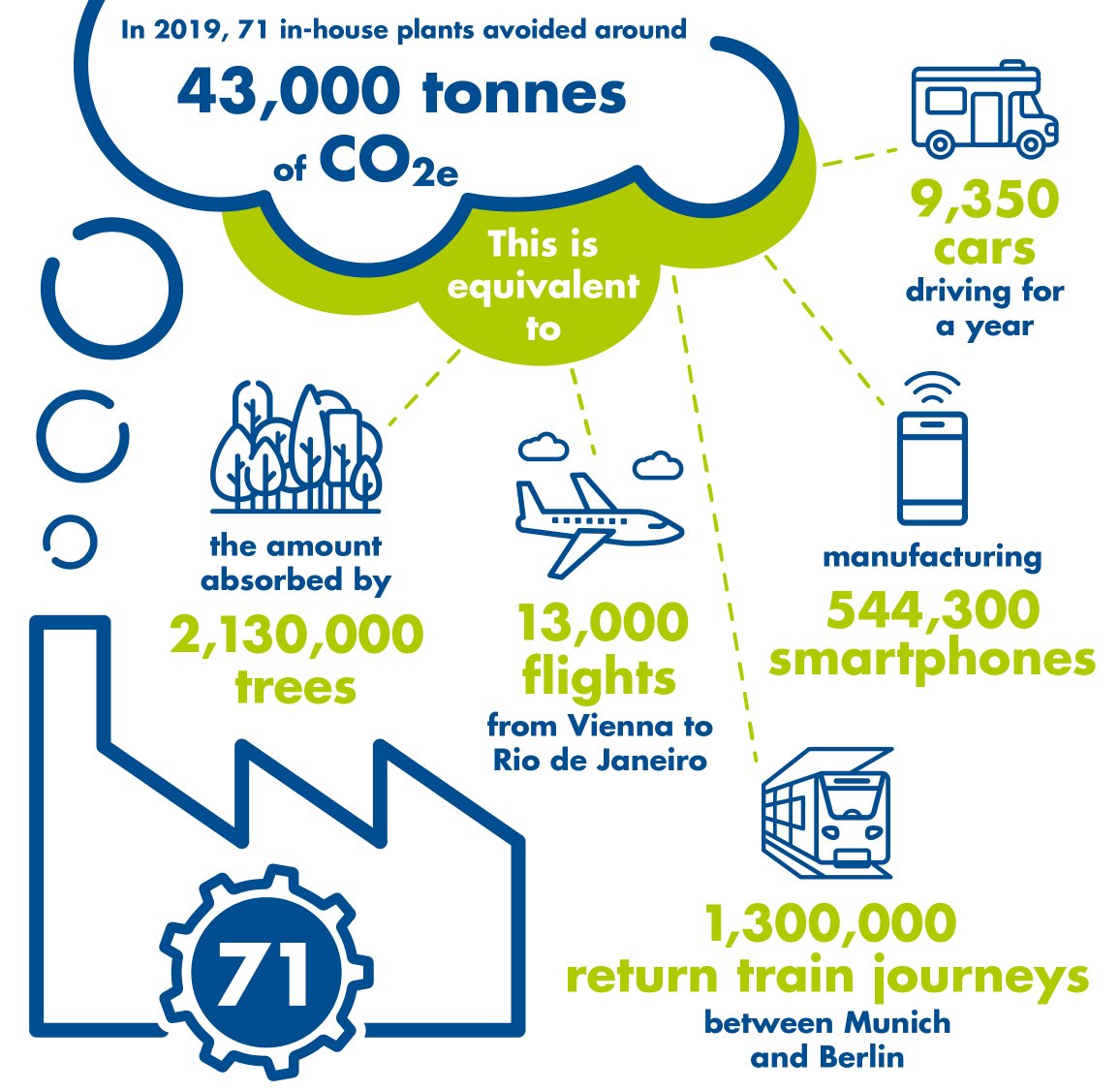
Use the savings potential systematically
But how did this avoidance of 43,000 tonnes of CO2e come about? ALPLA in-house plants can be found directly in or right next to our customers’ facilities. Here, packaging is literally produced right next door to the bottling facilities. Where a lorry would normally come along, load the preforms or packaging and transport them to the customer, the packaging speeds off directly to the bottling facilities via conveyor belt. ‘No outer packaging is necessary for transport and the lorry is not applicable any more,’ explains Christian Buchgraber, Director Corporate Logistics at ALPLA. ‘In addition to that, we develop tailored logistics solutions with our customers, such as just-in-time production, automated storage and the optimum interplay of just-in-time production and automated storage.’ This results in an especially efficient collaboration with positive effects on the environment. ‘In-house production doesn’t just minimise greenhouse gases, but costs as well and enables a close and mutually successful collaboration between us and our customers,’ the logistics expert sums up.
In-house plants as a role model
ALPLA operates one of these in-house plants for Arla Foods UK in Aston Clinton in the UK. The plant meets the very latest requirements in terms of energy consumption and the degree of automation. The decisive factors here are reduced compressed air consumption and a sophisticated infrastructure and warehousing technology. The entire process is fully automated. The bottles are produced by means of EBM technology on BMU machines made by Soplar, ALPLA’s main machinery supplier. This machine platform is one of the most energy-efficient in the world and boasts low energy expenditure during material processing and minimal production waste. Milk bottles made of HDPE, however, weigh around 20 per cent less than standard bottles and are produced using as high a proportion of recyclates as possible. You can find further information on this plant in the UK and on in-house logistics in our sustainability report.
ALPLA opened its very first in-house plant for Henkel in Lomazzo, Italy, in 1985. The close proximity to the customer and the resulting contribution to climate protection have been part of ALPLA’s company philosophy for more than 35 years.
Do you like our texts? Perhaps even so much that you want to use them in your own media? Then please get in touch with us beforehand!